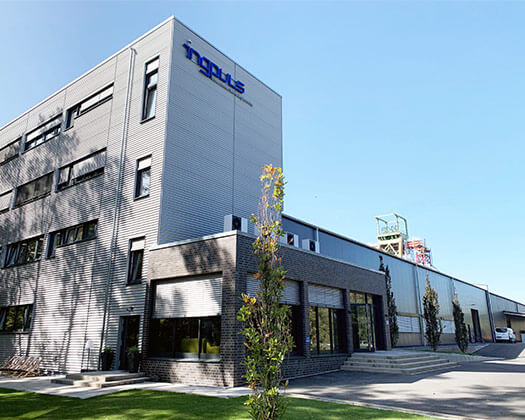
From the discovery of SMA to your new possibilities
The shape memory effect was discovered by A. Ölander in a gold-cadmium alloy as early as 1932. In 1963, then, the Naval Ordnance Laboratory achieved a breakthrough with nickel-titanium in the USA. Since then, the research intensity has proceeded in wave-like movements. In relation to the tens of thousands of patents that were created, only a few solutions proved feasible in the past. With its high level of expertise in this field, Ingpuls GmbH stands out as a unique supplier worldwide.
For the first time, solutions based on SMA are conquering markets across all industries – with a whole new level of maturity – and are displacing established solutions: A new wave that is finally bringing real products in its wake.
Complexity down to the last atom. What are the challenges?
The breakthrough was lacking in the past for several reasons. Firstly, there was a lack of a fully integrated suppliers that represented the entire industrial value chain from development to installation in functional solutions. Secondly, SMA requires absolute specialist knowledge in all areas concerned: With SMA it is important to understand the extremely complex interrelationships of material composition (alloy) and
processing (melting and heat treatment to the semi-finished product) whilst being fully aware of the customer’s installation situation and its operating conditions. Even the smallest deviation in any one of these areas resulted in products that cease to function.
How to make the most of your possibilities with SMA
As a consequence only a fraction of the potential of SMA has been reached to-date. Used correctly, SMA offers you a huge opening in your market – your possibilities are manifold and almost unlimited as SMA is a cross-sectional technology. With Ingpuls, as a fully integrated solution provider for functional materials made of SMA, you now have the chance to tap into extraordinary innovation opportunities on the market. Because Ingpuls masters the material-specific complexities like no supplier before – and all under one roof. All you need to do is tell us your requirements. Would you like to talk about your project now and give your imagination free rein? Then contact us now!
Your introduction to SMA
The more you understand the basic properties of SMA, the more likely you are to identify and filter out the best of your ideas and concepts. We offer you seminars and webinars in which you can learn the technical basics of SMA – at our office, at your premises as an in-house seminar or fully digitally without travel costs and
and CO2 emissions in the form of a webinar. Or would you like to get going straightaway? We invite you to engage with the SMA topic and discover your new potentials. Should you have any further questions, we will be happy to assist you – just contact us!