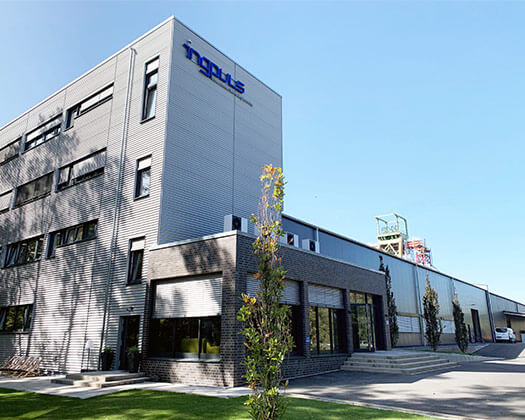
Shape memory alloy as a technology – what’s behind it?
Our products are used in many different areas. From household appliances and medical technology to aerospace. Behind all products is the same smart technology, called shape memory alloys. Shape memory alloys which, due to their special composition,
can take on key functions in modern technological applications. They can replace existing technologies or enable functions that cannot be implemented with conventional solutions under given boundary conditions.
SMAs are defined by the fact that they can return to a defined shape after a seemingly plastic deformation.A distinction is made here on the basis of the physical variables that cause a shape memory effect:
• Mechanical: Superelasticity / Pseudoelasticity
• Thermal: Two-way effect
• Thermomechanical: One-way effect
All shape memory effects are based on a solid-state phase transformation, better known (or also known) as the martensitic phase transformation. A martensitic phase transformation is a diffusionless homogeneous lattice deformation. Based on the type of phase transformation, the low-temperature phase in shape memory alloys, as is known for steels, is called martensite.
The high temperature phase is called austenite. The different effects that result from solid-state phase transformations make it possible to use them for technical systems in an intelligent way that is adapted to the respective need. At Ingpuls, we primarily produce and use nickel-titanium-based shape memory alloys, also known as Nitinol.
In comparison to other shape memory alloys, Nitinol SMAs most desirable properties are high wear and corrosion resistance and biocompatibility.
Pseudoelasticity / Superelasticity
Pseudoelasticity, also known as superelasticity, describes the ability of a metallic material to be subjected to elastic/reversible strains in orders of magnitude way above the elastic strains that a conventional steel can assume. In the case of pseudoelasticity, the material is in its high-temperature phase, austenite, at the application temperature. The component has thus already assumed its defined shape. If it is subjected to mechanical stress, at a critical point the material undergoes stress-induced transformation to martensite.During the process, martensite variants are formed that are oriented favourably to the direction of the strain. The formed “twinned martensite” provides the effect path, which macroscopically manifests itself in a large strain. When the material is unloaded, this transforms back into austenite. Since austenite only permits lattice modification, the material reshapes itself into its original shape during the course of the unloading and the associated transformation.The behavior is comparable to that of rubber. Pseudoelasticity is used primarily in medical technology. For example, stents made of pseudoelastic shape memory alloys can be guided through microcatheters due to their great elastic stretching capacity. When the stent reaches the vessel to be supported, the catheter is withdrawn, and the stent can fully expand and support the vessel wall where it will survive the cyclic strain of each heartbeat for many years to come.
One-way effect
In the one-way effect, a material is seemingly plastically deformed in its low-temperature phase and then returns to its original shape when exposed to heat. The low-temperature phase martensite is characterized in shape memory alloys by the presence of certain crystallographic regions within the martensite grains, so-called twins. If a component is subjected to a stress as a martensitic phase, from a critical stress onwards twin variants that are favourably located to the stress direction grow at the expense of other variants.In this case, the material can be deformed at a low stress level. In the high-temperature austenite phase, there is only one way in which atoms can arrange themselves in the lattice. Thus, when heated above a critical temperature, the material reshapes itself into its original shape and remains in this shape even after cooling into the low-temperature phase without the influence of a mechanical stress. Therefore, in order to take advantage of this effect in cyclic applications, an external mechanical stress is needed to deform the component into a different geometry when cold. This is known as the extrinsic two-way effect.
Two-way effect
The extrinsic two-way effect is used, amongst others, in thermostatic valves. Here, an SMA compression spring works against a spring made of conventional steel. When cold, the steel spring applies a force high enough to compress the SMA spring. When warm, the SMA spring “remember” its longer shape and thus applies a force that can compress the steel spring. This effect can be applied form over 100.000 cycles if designed and manufactured properly. The temperatures that produce the effect are adjustable by allow composition, microstructure and design layout.
What are the main areas of application for shape memory alloys?
Are you interested in our SMA webinar?
Gain in-depth knowledge in your area of application