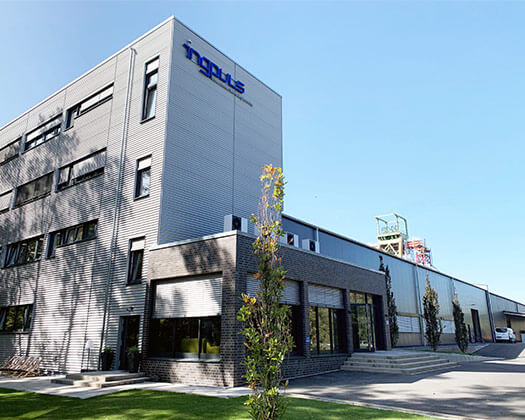
What is meant by Nitinol in terms of SMA?
The first observation of a shape memory effect was made by A. Ölander in the early 1930s on an AuCd alloy, which, however, could not be explained at that time. It was not until 1963 that intensive research on shape memory alloys was triggered by a chance discovery during research on heat shields. As a result of this discovery at the Naval Ordnance Laboratory (Maryland, USA), the shape memory alloys based on nickel and titanium with the highest technological significance to date now have
the trade name Nitinol. To date, the largest area of application for Nitinol has been in medical technology. A few years ago, about 90% of NiTi applications were found there. It was here that the cardiological stent was produced as the first mass-produced product. Due to its pseudoelastic material behavior, it can be passed through a microcatheter. When it emerges from the catheter in an artery, it resumes its original shape and can thus keep the vessel open and prevent it from
reoccluding. This treatment method is used, for example, in cases of arteriosclerosis, a hardening of the arteries. Nitinol is also used in the dental industry (e.g. root canal files), surgery (surgical tools) and orthopedics (orthoses).
Impurities in Nitinol production
The slightest impurities can have a negative effect on the production of Nitinol alloys. However, these inclusion levels can nowadays be significantly reduced by special melting and processing methods. To assess the purity of nitinol in relation to industrial applied manufacturing processes, the 2015 technical scientific publication by Scott Robertson et al. is an important reference in the nitinol market (Scott W. Robertson, Maximilien Launey, Oren Shelley, Ich Ong, Lot Vien, Karthike Senthilnathan, Payman Saffari, Scott Schlegel, Alan R. Pelton,
JMBBM 2015 p119-131). Impressively, Robertson demonstrates the role of inclusions in assessing the functional fatigue of nitinol. Smaller inclusions, larger inclusions, and smaller numbers have a large statistical effect on fatigue behavior in superelastic wires and tubes made of nitinol. Other publications demonstrate the positive effect of smaller precipitates on corrosion behavior (Harshad M. Paranjape ∗, Bill Ng , Ich Ong , Lot Vien , Christopher Huntley ; Scripta Mat 2020 p442-446).
Their equally positive influence on fatigue behavior has also been scientifically documented (using stents by way of an example, Fan Sun, Laurence Jordan, Valérie Albin, Virginie Lair, Armelle Ringuedé, and Frédéric Prima, ASSODF 2020 p3073-3079). For exciting insights on the topic, check out our Medical Technology Insight Talk.
What are the effects of impurities in Nitinol?
The level of impurities in nitinol production is decisive for the quality of the shape memory alloys. This has a significant influence, for example, on the service life of permanent implants or the actuators used in cars.
The impurities in nitinol production are decisively influenced by the control of the melting process as well as the purity of the raw materials. Furthermore, chemical changes within the nitinol material have an impact on the corrosion behavior. In order to avoid impurities of this kind, it is important to carry out careful controls in the production of nitinol and to ensure that the manufacturing process is carried out cleanly.
How do impurities arise in nitinol production?
Hydrogen, nitrogen, oxygen or carbon can cause relevant impurities during the production of nitinol. If these elements – primarily oxygen and carbon – are present in comparatively large quantities in the material, precipitates form in the nitinol. This results in the formation of either titanium capides or titanium oxides, which lead to brittle behavior in the ductile nitinol. Consequently, the quality of the nickel-titanium alloy is significantly influenced by this type of contamination. If a Nitinol implant contaminated in this way is subjected to mechanical stress, a crack may already occur if a brittle particle is present on the surface of the filigree structures of the Nitinol implant. The consequence would be failure of the component.
Quality factors of Nitinol alloys
The quality of shape memory alloys or Nitinol is based, on the one hand, on the purity of the raw materials and on the correct execution of the melting process during production. On the other hand, the composition of the alloy also plays a major role in material quality in nitinol production.
The composition of shape memory alloys is determined in terms of the required properties that the finished product should meet in order to achieve the desired shape memory effect. These properties can be divided into mechanical properties, thermal properties, surface properties of the metal and functional properties.
Explanation of the quality factors
While mechanical properties refer to the force a shape memory material builds up or the degree of deformation of a component, the thermal properties of the shape memory alloy, on the other hand, include all properties with respect to temperature. This also includes the deformation aligned to temperature as well as the response of the shape memory alloys. The surface properties of the metal are examined under a microscope for specifications met during the manufacture of the shape memory alloys. The functional properties describe the mode of operation according to which a component acts. Here, it is important to specify and understand the fatigue of the shape memory alloys with pinpoint accuracy. The correct production of the shape memory material is the decisive factor for the lowest possible and precalculated fatigue of the final component.
Quality factors of shape memory alloys or Nitinol
When talking about the quality factors of shape memory alloys or Nitinol, they cannot be reduced to one factor or number. Instead, the quality factors of shape memory alloys describe a sum of many different factors. The four factors described above are further supplemented by the quality of the packaging and the documentation. These come into play in the automotive industry, for example. Here, the classification of the goods play a crucial role in the use of the products. Faulty labeling consequently means a lack of quality assurance, as a result of which the component cannot be used.
Semi-finished products made of Nitinol
Nitinol can be produced and processed in various forms. The product resulting from nitinol processing is called a semi-finished product, which, unlike a finished end product, is an intermediate step in production. Wires, sheets or powders are different semi-finished products that can be made from Nitinol. The production of any semi-finished Nitinol product starts with the same step: the production of the ingot. After a specific composition for the Nitinol alloy has been determined and the individual elements have been weighed accordingly, they are first put into a furnace; a vacuum induction furnace, for example. By heating to about 1350 degrees Celsius, the elements liquefy and form a nitinol alloy. Next, the metal, which is liquid at this point, is poured into a steel mold to form a cylindrical body: the ingot. The mushroom-shaped form of the ingot head is necessary so that a blowhole (air bubble or hole) forms in this head, and this in turn does not form in the component itself. The mushroom-shaped head is finally cut off, leaving the cylindrical body made of nitinol, which can then be processed further.
Further processing into semi-finished nitinol products
Forging is one possible way of further processing the ingot into semi-finished nitinol products. Forging produces a rod which, as a semi-finished product, offers a wide range of additional processing options. One of these possibilities for further processing of the semi-finished nitinol product is the tube. If the resulting tube is drawn further, it can be processed into a stent. If, when processing the rod further, the hole for the tube is dispensed with and the rod is instead drawn on directly, this step is known as the wire drawing process. Wires can be produced on the basis of the nitinol semi-finished product, which can have different thicknesses. Rectangular castings, for example, can also be used to produce ingots, which are rolled into thin sheets in further processing. To produce SMA powder, an electrode must first be machined out of the original Nitinol ingot.
Manufacturing process for Nitinol alloys
In the production of shape memory alloys or Nitinol, almost every manufacturing process known to us can be used, so that every conceivable semi-finished product can also be produced as a Nitinol semi-finished product. In this way, the end user can determine in advance which Nitinol semi-finished product is required for the manufacture of the end product. From casting to the semi-finished product ready for sale, however, production usually involves several hundred processing steps, so that the individual processes should be precisely coordinated with each other and, of course, in line with the customer’s requirements.
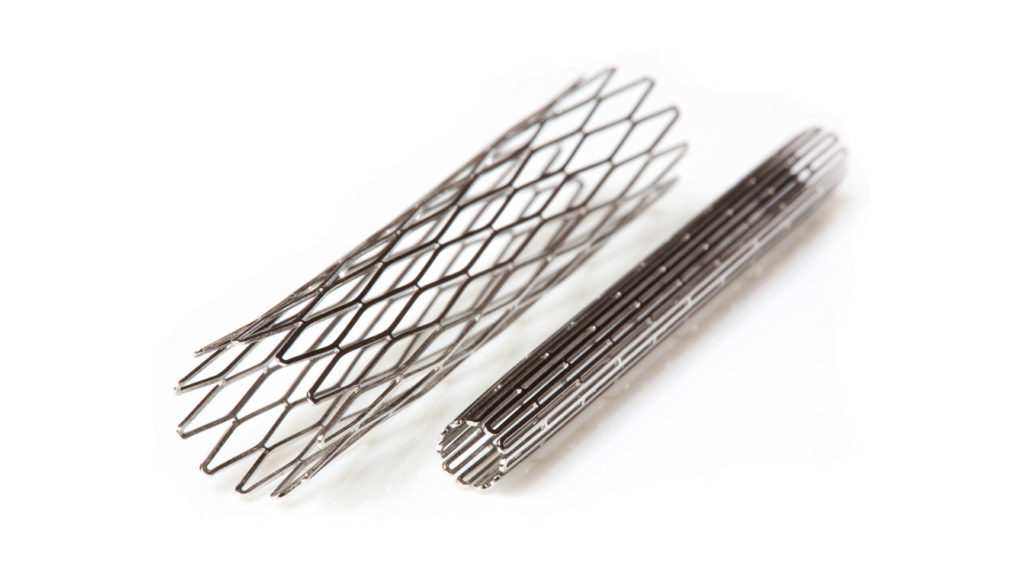