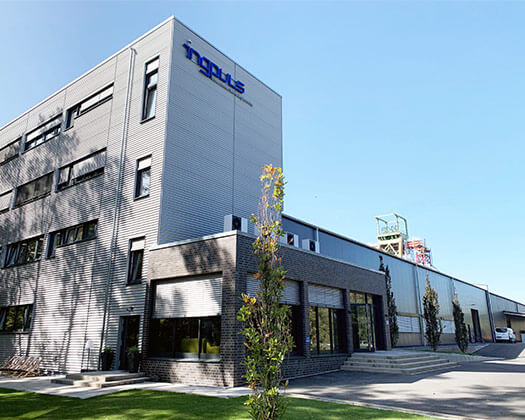
Benefit from the virtually unlimited possibilities which thermal coatings with shape memory alloys (SMA) can offer you. Irrespective of your purpose: Challenge us with your request!
Your benefits through SMA coatings
High tech in its purest form: That is what thermal coatings based on shape memory alloys are. And now you can benefit multiple times from this truly cross-sectional technology: You will be able to increase your productivity through an endless spectrum of technological possibilities. Thermal shape memory alloy coatings are already considerably reducing tool costs and extending the service life of our machines in our own repair shop. But our customers have also identified thermal SMA coatings as a true driver to innovation. That’s where it comes to you: What type of project are you working on? How this works exactly with shape memory alloys will stay our secret for now. Therefore, let’s first find the best process for your challenge (or for your project) from the range of possibilities open to you!
Application of SMA coatings
Whatever your needs are protection from wear, reduction of vibration, increase in efficiency or optimised performance parameters: Thermal SMA coatings are the key for your next leap in technology, because in the case of thermal coating with SMA, the improved material properties of your products result from the functional surface. This is created selectively and locally according to your requirements: Thereby you will receive your defined mechanical and physical properties, and thereby often create not only an improvement but a completely new, enormous potential for application.
A thermally coated surface forms a connection with the substrate without any added heat being supplied. This creates the ideal protection for your components that are subjected to high mechanical or thermal stress; precisely according to the load profile of your request. When applying thermal coatings in shape memory alloys,
you will profit from not only technical benefits but many others: From our understanding of the process in its interdependencies with the materials, our know-how originating from our own in-house production and from the profound understanding of applications that we can apply to your technical challenges.
Truly unique for thermal SMA coatings is, that you will receive your solution from the onlyprovider who controls the full process chain from the SMA melt through to the delivery of your finished coated component.
The chance to benefit from shape memory alloy coatings
us sectors, as a key technology, functional SMA coatings make it possible to solve virtually any of your challenges in the field of coatings. The technical solutions will elegantly work as functional material with improved material properties paying off across the board. Do you want to know your possibilities? Then get in touch with us now
Robust and resistant SMA coatings provide your products with an increased capacity for thermomechanical load and a better environmental performance: Reduction of vibration reduction, improved temperature resistance, optimised resistance at higher loads and stresses: This allows your components and assemblies to be exceptional within the product life cycle of your customers, based on their excellent reliability and durability.
Where do you want have the edge over your market leader? Nowadays, billions of industrial components are functionally coated. With thermal coatings based on shape memory not only to you refine but you can integrate completely new functions, skillfully combine technical properties and create real added value. Whether you want to coat complete surfaces with a uniform coating or prefer to coat partial areas – right where your components are subjected to high loads – that’s where you can achieve a sustainable advantage through innovation. Where do you want to create innovative surfaces that are functional and capable Your customers will benefit from shape memory alloy coatings in many ways. Whether your products are exposed to high wear, or you are looking to reduce the risk of corrosion; if it is the thermal resistance or the thermal expansion of your solutions that is most critical; whether biocompatibility is important to you or whether you need to optimise the electrical parameters. We will work out the perfect solution for you and select the ideal SMA-based thermal coating for your requirements. In the following overview, you will be introduced to an almost unlimited array of possibilities; here we show you the most common advantages and examples of thermal coatings with shape memory alloys. Find out why you should get in touch with us now. Our customers from a wide cross-section of industries are benefitting from thermal coatings with shape memory alloys. Their products are often used at the limits of performance: Whether under high mechanical load or under adverse application conditions. In these areas, thermal SMA coatings provide you with real benefits; specifically used in a functional manner and exactly where you can achieve a real leap in innovation with your product. Find out more about this emerging subsection of additive manufacturing! The thermal coatings are not only available as a service (coating services): If you prefer – according to your requirements – we can provide excellent coating engineering. This allows you to experience cost-optimised precision and high-quality solutions designed for your individual application and special use cases. Individuality, precision, quality: You can now profit from our knowledge and skills which we have used for a long time in the coating of tools in our own production: We are happy to confirm your trust in our competence. Approach us now with your technical challenge!
In which area do you manufacture products with the highest quality standards?
Advantages and examples of thermal coatings from shape memory alloys:
Sliding coating, anti-stick coating or protective coating: General overhaul instead of replacement, avoiding layer adhesion (mechanical jamming or adhesion) and cold-welding phenomena even with foreign particles and in the case of material combinations, resistance to erosion and cavitation, suppressing triboluminescence, reducing friction, preventing material fatigue and abrasion caused by vibration.
Your benefits: Significantly extended durability of the substrate, low-maintenance designs, reducing shutdowns/increasing productivity, longer machine running times, for example in the mining industry, in industrial valves, in highly stressed rollers, bores and seats in bearings, in axles or shafts, in brake discs or synchronous rings, in ship screws or in exhaust systems optimised against wear
Corrosion resistance: Extended durability of your components, reduced repair requirements and more degrees of freedom in the design: Preventing galvanic corrosion (such as pitting corrosion in connection with electrolytes and oxygen deficiency), in which the anodic part is attacked, and also in the suppression of high-temperature corrosion, in which oxygen corrodes the metal over a long time and at high temperature.
Your benefits: Reduced maintenance costs, more durable use, for example in gas turbines, for downsizing internal combustion engines, in exhaust systems or in cylinder coatings.
Allows higher operating temperatures without compromising functionality and opens up new application areas for your components, machines and installations, for example in the case of thermally insulated gas turbines. Your benefits: Higher operating speeds can be achieved, warmer operating points can be attained.
Better sealed rotating machines, better fitting coatings in highly stressed parts and selective coatings with different diameters (for example in bearings and rollers).
Your benefits: Better fitting bearing seats, faster rotating speeds of rollers and mills (e.g. paper/steel industry), cost-efficient restoration, mechanical seals (e.g. in industrial valves).
Achieving precise target properties such as conductivity, insulation or magnetism, at designated locations, without interacting adversely with the substrate.
Your benefits: Functional integration, electrical shielding, safety against electrical shock.
Structures with refined surface areas, partial input, functionally refined structures, longer durability of medical applications, with simultaneous neutral interaction with the body’s own bio system and intact substrates, i.e. without melting of the surfaces.
Your benefits: Functional improvement and weight reduction, cost savings in large and small series, longer durability of prostheses and orthoses, for example in orthopaedic and surgical applications.
Production of very good traction properties such as roughness or targeted surface profiles, haptically optimised coatings, can be used partially or wholistically in your component.
Your benefits: Functionalisation of surfaces optimised for traction, for example, optimising of running surfaces of rollers and sealing strips.
Essential in modern lightweight construction: Components and systems with highly functional finishing, while simultaneously optimizing function.
Your benefits: Allows significant leaps in innovation and weight savings with improved product quality, for example in the field of aerospace in turbine blades.
Wherever high performance, durability or special haptics are required, for example in hydraulic applications, in mining or in oil and gas. In any other application areas merely the SMA additive, being composed of a wire or powder additive, is heated to a plastic or molten state. The substrate retains your pre-set properties and is optimised locally by means of thermal coating.
Your benefits: Optimised function only where it is required, for example in selective coating of moulding rollers in the food industry, for rollers with different diameters or in coating of industrial valves.Important final words: