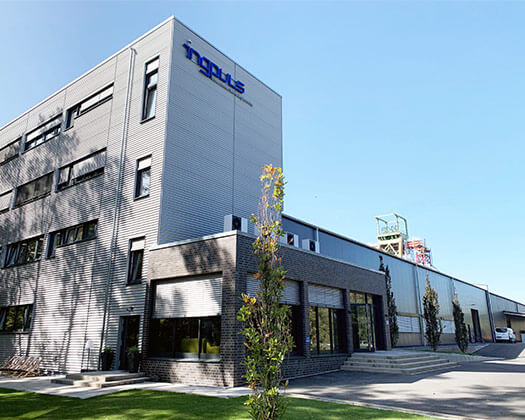
What is Additive Manufacturing?
Additive Manufacturing refers to a manufacturing process in which components are built layer by layer from digital models—rather than being created by milling, drilling, or casting as in traditional methods. This process is better known as 3D printing.
In contrast to subtractive manufacturing, the workpiece is created through material deposition instead of removal.
Basic Principles and Functionality
The process is based on a digital CAD model that is sliced into thin layers. A machine then builds the component layer by layer, typically by:
- Melting powder (metals, polymers)
- Extruding thermoplastics
- Curing resin using laser/UV light
The result: a highly customized component with often complex geometry that would be impossible to manufacture using conventional techniques.
Additive vs. Subtractive Manufacturing
Additive | Subtractive |
---|---|
Material is added | Material is removed |
Minimal material waste | High material loss |
Complex geometries | Limited design freedom |
High customization | Optimized for mass production |
Additive Manufacturing offers clear advantages, especially for small quantities, prototypes, or complex internal structures.
Technologies in Additive Manufacturing
Typical technologies include:
- Selective Laser Melting (SLM): Metals are selectively melted using a laser
- Fused Deposition Modeling (FDM): Plastic is extruded layer by layer
- Stereolithography (SLA): Resin is cured with light
- Binder Jetting: Powder is fixed using a binder agent
Ingpuls uses Additive Manufacturing to produce functional prototypes and complex part geometries for shape memory alloys.
Fields of Application
Additive Manufacturing is used in:
- Medical technology: Implants, prosthetics, patient-specific instruments
- Aerospace: Structural components, engine parts
- Automotive industry: Cooling systems, lightweight components
- Special machine construction: Tools, end effectors
- Research & Development: Test systems with integrated functions
Advantages of Additive Manufacturing
- Design freedom: Complex shapes, cavities, and lattice structures
- Material efficiency: Less waste than traditional methods like milling
- Faster development: Accelerated prototyping
- Customization: Perfect for one-offs or patient-specific medical devices
- Reduced assembly effort: Parts can be produced in one piece
Additive Manufacturing at Ingpuls
At Ingpuls, we use additive manufacturing to develop innovative components based on nickel-titanium alloys (Nitinol).
Examples include:
- Functional prototypes for actuators
- Custom geometries for medical technology
- Tailored solutions in the field of smart systems
- Components with integrated shape memory effect