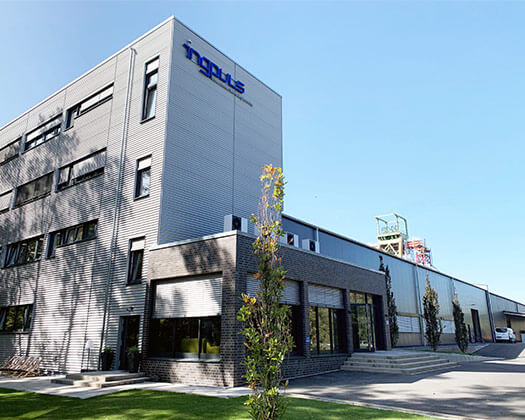
Shape memory components
You are not looking for a semi-finished product but – like the majority of our customers – would prefer a component or a finished system? In that case your semi-finished product will be subjected to additional processing steps. We will leave no stone unturned in order to manufacture your component in such a way that it meets with all your requirements. You can benefit from the fact that Ingpuls manages and controls the entire shape memory alloys value chain. This implies that even your greatest special requests can be realised using a large network of partners.
Examples for pseudoplastic shape memory components
Pseudoplastic shape memory alloys actuator wires provide highest actuating forces in your applications in the smallest and confined spaces. When the actuation temperature is reached, they will recall their original geometry at a time before their deformation (tension, bending, torsion). By undergoing this process, they execute large mechanical work expressed by their actuating force and actuating path. Pseudoplastic sheet metal elements made of shape memory alloys are primarily used as compact lifting actuators. Shape memory alloy sheet actuators are suitable for providing high actuating forces with moderate actuation paths in confined space. They are used either in a three-point bending support situation or as a cantilever arm being clamped on one side. However, your pseudoplastic actuator wires, sheet actuators and much more can also be customised for you: Depending on the application, these may consist of standard or special alloys: Thus ensuring that your shape memory alloys component reacts in a way that is suitable for the stresses and functions of your particular application.
Examples for pseudoelastic (superelastic) shape memory components
Superelastic components are often used in medical technology. Although they are made of metal, they can be bent, stretched and distorted like rubber yet they can always return to their original shape – without heating: A highly flexible metal, being up to 100 times more deformable than conventional steel. In this case, when increasing temperature, you are not trying to induce a change in shape into an earlier determined shape: Instead, in the case of superelastic shape memory components, austenite as the high temperature phase is already present at room temperature (or ambient temperature, or operating temperature). Thus, superelastic shape memory components can to a certain extent be viewed as pseudoplastic components which have already surpassed their transformation temperature at the prevailing temperatures.
The purpose of pseudoelastic shape memory alloys therefore is different: Namely that you can reversibly deform the material mechanically. This behavior is often required in medical technology. Outside of medical technology, two properties are particularly interesting: When used as a spring, the material exerts a constant spring force with extremely low spring stiffness, resulting in a constant force independent from the deflection of the spring. And in other applications, this behavior allows you to reduce vibrations by mechanically inducing deformations (more on this in the section SMA Academy Characterisation).
Where can pseudoplastic and pseudoelastic shape memory components be applied?
The following PDF document gives you an insight into the different applications:
Pseudoplastic and pseudoelastic SMA components as PDF
In order to convert a semi-finished SMA product into a shape memory component exhibiting your specifically required properties, various shaping processes are carried out. The forming methods include a mechanical part and process-related heat treatments. The mechanical part consists of processing steps which you will be familiar with. As a result, you will obtain moulded parts in a 2D or 3D configuration. The heat treatment (HT) on the other hand is aimed at setting your desired material properties and function parameters. Thereafter a final heat treatment takes place. If this final process step – referred to as shape setting heat treatment – is not undertaken at Ingpuls (e.g. you merely order cold-drawn wires), a targeted HT is required at your premises in order to set the functional properties of the material. The following table provides an overview of common methods which can be used for your desired components.
Available components
Your component is developed individually for you and based on the know-how of Ingpuls, which covers extremely complex interdependencies within the area of shape memory alloys. This means that you are able to choose from a variety of geometric shapes whereby you should generally distinguish between standard components and special components for actuator systems (actuator elements). Special components for actuator systems exhibit additional properties.
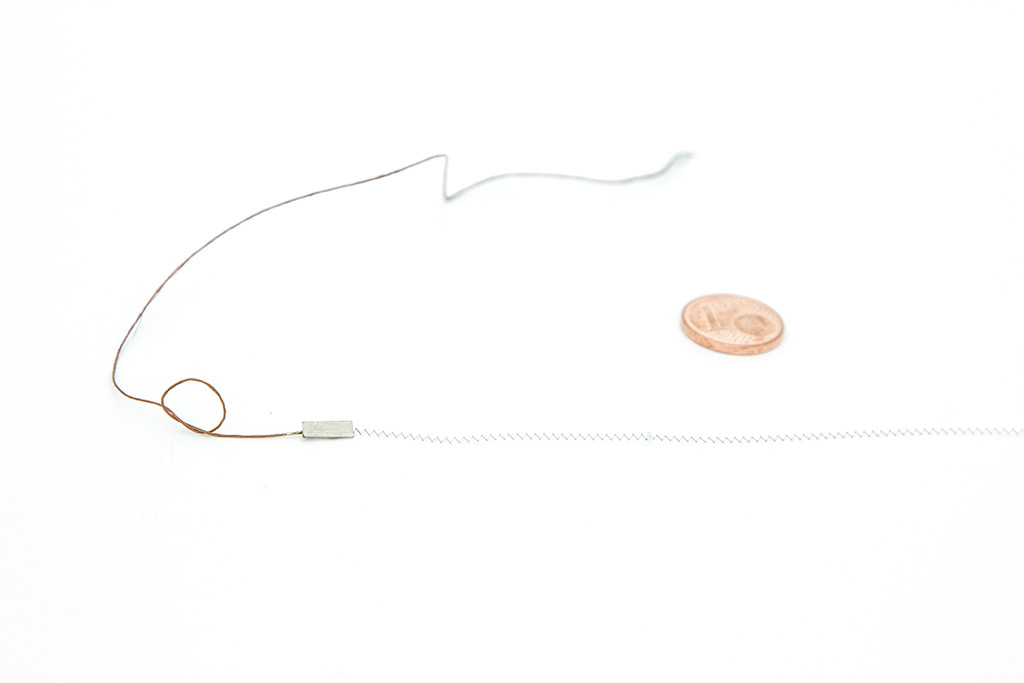
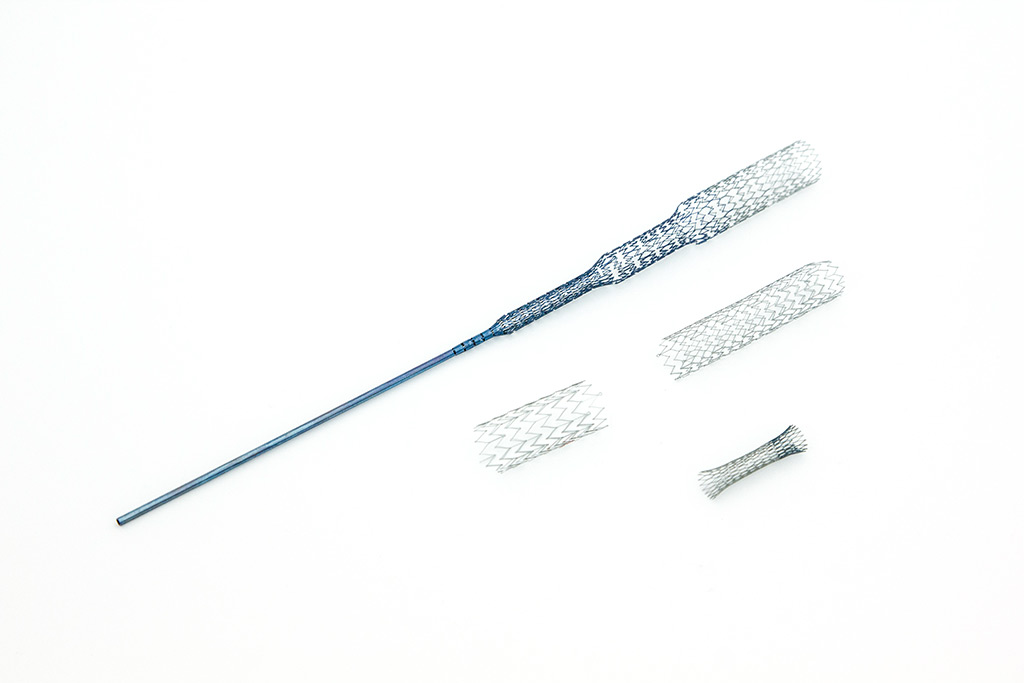
Please find below a list of available standard components available. It also tells you which type of semi-finished product they’ve been made of:
Portfolio of standard components as PDF
If you can see yourself benefitting from using standard components and actuators, just imagine the possibilities opening up for you using shape memory alloys for an individual project and customized solution!
Components surfaces
NiTi based shape memory alloys exhibit a thin oxide film of TiO (titanium oxide) due to their production process – unless they are heat-treated in vacuum installations. This layer has an auto-passivating effect and thus protects against corrosion; moreover, it improves the bio-compatibility. Nevertheless, some customers prefer processed surfaces. This may be for purely aesthetic reasons – as is often the case in medical technology – or also for technical reasons, possibly because your components will be subjected to cyclical loads: The reason being that in greater technical load conditions, cracks will always start forming on the surface. Hence a good surface quality will significantly increase the service life of your components. Please find below a list of surface processes and qualitative pricing in ascending order.
Surface processing method | Costs (qualitative) |
Mechanical grinding | + |
Mechanical polishing | ++ |
Sandblasting | +++ |
Trowalizing / Vibratory finishing | +++ |
Pickling | ++++ |
Electropolishing | +++++ |
As you can see, you can choose from a wide variety of options. And based on a deep understanding of shape memory alloys, your ideas can be converted to tailor made solutions: With Ingpuls controlling the entire process chain, it is also possible to exert an influence on the value creation process at any point. This means that in the end your shape memory alloy components will actually achieve the required effect as set out by you from day one.
How to incorporate your requirements into your components
You can see that it is vital that we understand your requirements for your components from day one in order to develop the correct alloy and component for you. You may not be aware that the installation of your component or solution can have a major impact on the functionality of your parts. Therefore, it is highly recommended that you prepare and forward to us a concise list of requirements. Should you wish for us to sign a non-disclosure agreement, then we would gladly enter into a contract with you as it will help both sides. Both parties benefit from an open exchange, ensuring a target- and solution oriented open discussion. It increases the chances of successfully generating the right SMA solution for you. Please complete our standardized questionnaire to record us of your requirements. This will ensure that:
- you will significantly reduce the response time to your inquiry
- you will receive a qualified answer in all cases: Even if it turns out that your requirements may not be met by using shape memory alloys
- you can ensure the integrity of your data.
- you may receive a solution which corresponds fully with your requirements
Generally, you will be given the option of signing a non-disclosure agreement on point of contact. And at the same time, you will normally receive the questionnaire regarding your technical requirements.
Individual actuator elements based on shape memory alloys
For newly developed products and solutions, individual actuator elements can be produced as a component that meets the requirements for your pre-defined installation space, while at the same time achieving the required actuating forces and actuating paths. If necessary, we can support you in the design and testing of actuator elements based on shape memory metals. If you prefer application-specific systems and complete actuators based on NiTi-shape memory alloys instead of components and elements for actuator systems, then you might want to take a look at the following page (systems and actuators).