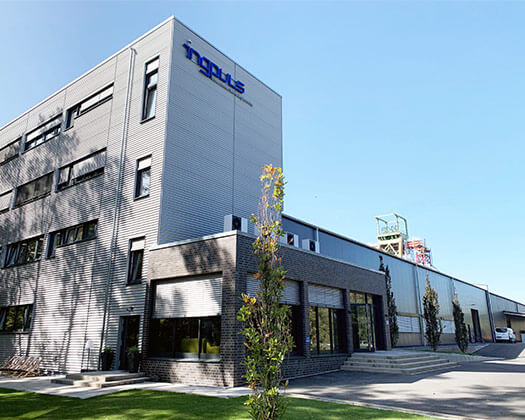
What are shape memory alloys?
Alloys based on shape memory technology are metallic materials that can remember their original shape after an seemingly plastic deformation. The terms memory metal, shape memory metal or even shape memory metal alloy are also widely used. Strictly speaking, however, these are not correct, as shape memory materials are alloys and not pure metals. Alloys based on nickel and titanium (NiTi, Nitinol) are particularly relevant in shape memory technology. Due to their functional properties, shape memory alloys are ideally for applications in actuator technology, but also for components which must be
capable of large reversible deformations (e.g. guide wires or catheters in medical technology) where reversible strains between 6-8% can be achieved. At this point we should take a closer look at the technology behind shape memory alloy, what exactly is behind it? The cause of this behavior is a solid-state phase transformation in the metal between two crystal structures, which are called martensite (low-temperature phase) and austenite (high-temperature phase). Depending on the alloy composition, ambient temperature and stress condition, different effects
can occur, which technical systems can benefit from in various intelligent ways. SMA springs, for example, can automatically open or close valves when the ambient medium (air, water, oil) exceeds a certain temperature, the austenite start temperature. Tension wires can realize moderate travels with very large actuating forces. Under certain circumstances (wire diameter < 1.2-1.4mm), they are suitable for heating with special control electronics directly via the ohmic resistance of the wire.
Nitinol: nickel-titanium shape memory enhancements
Ingpuls works with nickel-titanium shape memory alloys. On the market, the trade name Nitinol is usually used as a synonym for nickel-titanium alloys. In addition to nickel-titanium alloys, there are other alloys with a so-called shape memory. Examples of these are copper-based or iron-based alloys. Due to special properties, nickel-titanium alloys have prevailed over other alloys in industry.
The development of shape memory alloys looks back on a long history. As early as the 1930s, shape memory materials were discovered as gold-cadmium alloys. While this discovery did not initially lead to any applications, scientists observed this effect until nickel-titanium alloy was invented some 30 years later.
In which industries are shape memory alloys found?
In the search for a high-temperature material, nickel-titanium alloy was first found in the laboratories of the U.S. military. However the development of the first applications of nickel-titanium alloys took place in the field of medical technology.
By now nickel-titanium alloys have been established in the medical technology market for around 25 years. For some years now, shape memory alloys and nickel-titanium alloys in particular have been opening up many other markets as a result.
Today, shape memory alloys can be found in many different applications. Probably the most famous applications of shape memory alloys are in medical technology. These are the so-called stent, brace wires and root canal files.
How are shape memory alloys characterized?
When you observe the shape memory effect, the ambient or operating temperature plays an essential role. Because depending on how this behaves in comparison to the properties of the alloy of the SM element, you can mainly observe two different effects: On the one hand the extrinsic two-way effect and on the other hand the so-called superelasticity.
From a physical point of view, both effects involve a phase transformation within the material. This is reversible and characterized by diffusionless shearing of the crystal lattice. The transformation takes place between a low temperature phase and a high temperature phase. The low-temperature phase is
called martensite, the high-temperature is known as phase austenite.
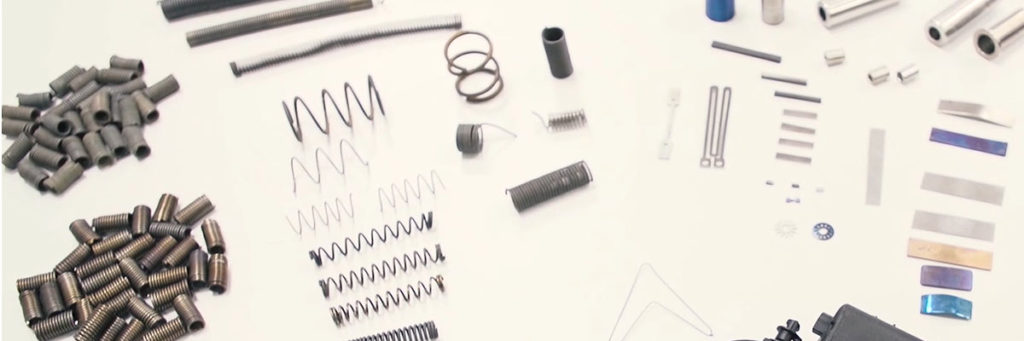
How do shape memory alloys work?
Shape memory alloys function by means of a so-called martensitic phase transformation, as is also known from steel materials, for example. Within the scope of this phase transformation, there are different crystal structures. Of importance for shape memory alloys are the martensite and the austenite, the properties of which also significantly characterize nickel-titanium alloys.
In shape memory alloys, a solid-state phase transformation takes place. Phase transformations per se are primarily known in relation to water: When water freezes, it becomes ice; when water evaporates, it becomes gas. A phase transformation takes place. This can be transferred to shape memory alloys, but in nickel-titanium the phases both remain solid. The actual phase transformation occurs inside the metal, by feeding or by increasing the temperature.
Solid state phase transformation of shape memory alloys
In reality, phase transformation looks like this: A wire consisting of a shape memory alloy can be deformed, bent or crumpled at room temperature, for example. If the wire is then heated above a very specific temperature, the shape memory is activated and it automatically remembers its old shape, which it then assumes again.
The exact composition of the respective alloy as well as the manufacturing process can individually define at which temperatures the material assumes which specific shape. In this way, for example, a straight wire can remain a straight wire. On the other hand, it can be determined during the manufacturing process that the wire should be a paper clip or a spring.
Superelasticity using the example of the stent
This effect is used in applications such as implanting a stent. To be implanted minimally invasively, the stent – the wire mesh made of nickel-titanium – must first be integrated into a very small catheter tube. While many other components would not survive this degree of compression, the superelasticity of the nickel-titanium alloy allows this severe deformation. Consequently, the superelasticity is used to place the stent in the catheter, so it can fulfill its task in the human body. As soon as the catheter sheath is finally retracted, the stent leaves the catheter and expands by itself. Because of this process, this application of the shape memory alloy is also referred to as a self-expanding stent.
Extrinsic two-way effect
In the extrinsic two-way effect, the initial shape of the material – after a seemingly plastic deformation by an external force (e.g. a steel spring or a weight) – is restored by heating. You should distinguish between a low-temperature phase (= initial position) and a high-temperature phase (heated state). In its initial position, the material is in the low-temperature phase where a martensitic metal structure prevails. You can now deform the material up to a certain point in all spatial directions, e.g. bend or stretch it. If you now heat the material above a certain temperature, a phase transformation takes place in the material itself: The martensitic structure transforms into an austenitic structure. The material is now in the high-temperature phase. This structural transformation from martensite into austenite takes place on a microstructural level and is invisible to the eye.
And it is precisely these microstructural processes that cause the material to return to its original state. Even when the material has been allowed to cool down again, it will remain in its original shape. And you can repeat this process a millions times – depending on the material composition and the degree of deformation – under ideal conditions the shape memory material will not be seen to fatigue. However, some form of fatigue will always occur at some point. If the component is properly designed and integrated into a system, however, operation can be reliably guaranteed. The name shape memory alloy comes from the observed shape memory effect.The initial state of the material thus always reflects the shape that has been written into the material’s “memory”.
This is where it wants to deform back to when heated. In addition, a so-called intrinsic two-way effect can also be observed, but for reasons of simplicity and lack of technical relevance we will not go into this. (usable strains and stresses are too low). Depending on your requirements, you can freely determine the “memory” of the material in advance. This is done by a specific heat treatment. Instead of the extrinsic two-way effect, however, shape memory alloys can also have another property called pseudoelasticity. The decisive factor is the temperature level prevailing in the material which derives from the environment or the operating condition.
Pseudoelasticity (also “pseudoelastic behavior” or “superelasticity”)
A pseudoelastic SMA element behaves like a rubber. When you hold a pseudoelastic SMA element in your hands, you can bend it like rubber with very little effort. All this with strengths that you know from metals. In the case of pseudoelasticity, you do not want to achieve a shape change back to the initial state by increasing the temperature. The material of pseudoelastic shape memory alloys is designed in a completely different way: It is then modified by the alloy in such a way that an austenitic microstructure is already present at room temperature (ambient temperature, operating temperature) – technically the high-temperature phase.
To a certain extent it is a shape memory material with a two-way effect with very low transformation temperatures. The material at hand has therefore already exceeded its transformation temperature at the prevailing temperatures. And that is the trick! Now you could cool the element below room temperature and produce martensitic microstructure as in the extrinsic two-way effect. However, the purpose of pseudoelastic shape memory alloys is different: Instead of cooling, you can mechanically deform the material. A transformation to a martensitic structure then takes place solely as a
result of your mechanically applied deformation. If you now relieve the element mechanically again, you will observe that the deformation recedes almost completely and the original shape is restored. The pseudoelastic effect of shape memory alloy is only possible because the austenitic phase is stabilized at room temperature. And just as with the one-way effect, this pseudoelastic deformation can be repeated millions of times depending on the design.
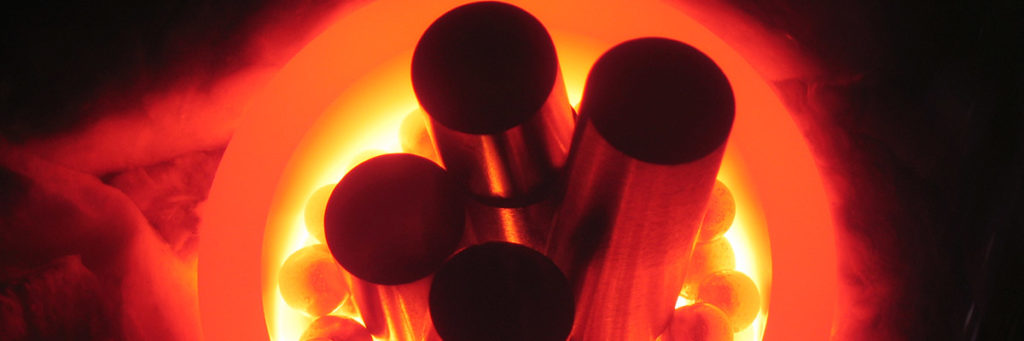
What are the properties of shape memory alloys?
Shape memory alloys (SMA) are based on the alloying elements nickel (Ni) and titanium (Ti). These are referred to as binary NiTi SMAs. The term binary comes from the fact that the alloy is composed of these two (binary = two) components. The following material parameters refer to this binary SMA.Pseudoplastic SMA: Pseudoplastic (thermally activatable) SMAs achieve strengths of more than 1200 MPa [N/mm²] and elongations at break of more than 10% in tensile tests.Pseudoelastic SMA: The material parameters of SMA exceed those of the normal tensile test. In the tensile test at room temperature, pseudoelastic SMA exhibit mechanical hysteresis. Thereby an upper plateau stress can be recognized. This is above 380 MPa [N/mm²]. With SMAs, the transformation temperatures are crucial. These are the temperatures at which a phase transformation between martensite and austenite begins or ends.
What are the advantages of shape memory alloys?
Unlike normal structural materials, shape memory alloys are functional materials. They are capable of integrating functions within their structure to replace engineering systems. For this reason, shape memory alloys compete with current technology standards, especially servo drives, solenoids or piezo actuators.
Compared to these technologies, shape memory alloys have decisive advantages: they are smaller and lighter, as less material is required to achieve the same performance. In this way, shape memory alloys simplify technological systems and applications.
In the context of an increasingly complicated technological world, shape memory alloys offer a comparatively simple alternative for developers and engineers. The use of shape memory alloys enables new approaches and optimizations that would hardly be possible with the original technologies. In the automotive industry, shape memory alloys contribute to more sustainable mobility with silent and space-saving application.
An example: the thermostatic valve
A concrete example at this point is the thermostatic valve. This has the task of regulating and controlling fluid circuits. In order to dissipate heat away from the engine and provide heat elsewhere, in the passenger compartment. In the past, thermostatic valves were illustrated with wax expansion elements. A wax expansion element consists of a kerosene wax, which is built into a metallic sheath. Within this shell, depending on the temperature, the kerosene wax expands and further activates the transmission of the force. Due to its complex structure, the wax expansion element is comparatively slow and significantly heavier than an SMA element. In a modern car, a slow shifting process and a heavy component mean a significant disadvantage for performance and functionality.
Shape memory alloys substitute wax expansion elements 1:1. They are usually up to 90% lighter than the previously used elements and at the same time up to ten times faster. The switching material is the element itself and can thus be placed directly in the cooling circuit.
Thanks to their special properties, shape memory alloys offer crucial advantages over conventional, technology-based solutions in various industries and play a particularly decisive role with regard to future developments.
Your introduction to shape memory alloys
The better you understand the basic properties of shape memory alloys or Nitinol, the more likely you are to recognize and filter out the best of your ideas and concepts accordingly. We invite you to explore the topic of shape memory alloys and discover your new potentials. You will find the all the relevant information you may need in the following sections (Characterisation, Properties, Manufacturing, Quality Assurance, Application, Webinar) at our SMA Course as PDF.