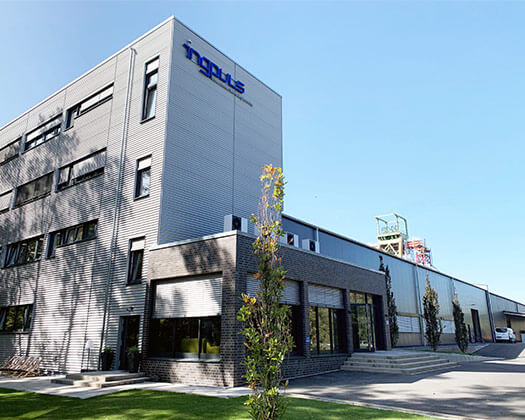
These are the mechanical & physical properties of Shape Memory Alloys
In this section you will learn about basic mechanical and physical characteristic and their key values that become relevant when you are dealing with shape memory alloys.
Firstly, you will find out about typical material properties for pseudoplastic and pseudoelastic NiTi SMA. Then, you will learn about the different predominant phases present in the material based on heating and cooling processes; being martensite and austenite. In addition, you will get to know thermal hysteresis. In the following, you will become acquainted with other factors which will have an influence on the fatigue behaviour of your shape memory alloy system. Finally you will gain insights about the biocompatibility and corrosion resistance of the material.
Do you want to understand the details of this section? You can download the entire course HERE. Once you have understood the basic principles, you may resort to the additionally provided summarised version, for reference and as a recap. Understanding the properties will greatly help you understanding our design as well as operational aspects. This will prove greatly beneficial to you: Think of what you will answer your customers when they start posing in-depth questions about your innovative shape memory alloy solution.
Mechanical and physical properties of SMA
If your SMA component consists of two alloying elements, is will be called a binary shape memory alloy. In a tensile test, binary NiTi SMA (composed of nickel and titanium) achieve strengths of more than 1200 MPa [N/mm²] and an elongation of over 10% at fracture (pseudoplastic version). Pseudoelastic SMA, however, display a mechanical hysteresis. An upper plateau tension is formed which lies above 380 MPa [N/mm²]. Further mechanical and physical properties that might be relevant for your application can be found out in a personal meeting.
Transformation temperatures: As, Af, Ms, Mf
As already mentioned, in SMA transformation temperatures are decisive. These are the temperatures at which the phase transformation between martensite and austenite starts or ends.
If you supply heat to your pseudoplastic component, the martensitic material structure converts into an austenitic structure. Here, the temperatures are relevant at which the conversion begins (As, Ms), ends (Af, Mf), or at which the rate of conversion reaches its peak (Ap, Mp).
When cooling down, your shape memory alloy component passes through these phases in the reverse order. However, it must be noted that the conversion processes do not run symmetrically, thereby displaying a phenomenon referred to as hysteresis. Therefore you will only be able to determine the current structural composition at a given point as long as you know from which direction you have been approaching the transformation process: Is it a heating process or a is the material in the state of cooling down? It is also noteworthy which phase components have been present beforehand since what happened during cooling depends on what happened during
previous heating. This behaviour is explained in more detail in the course by following a practical example. Download your course here to understand the importance and sequence of the characteristic values for the transformation temperature.
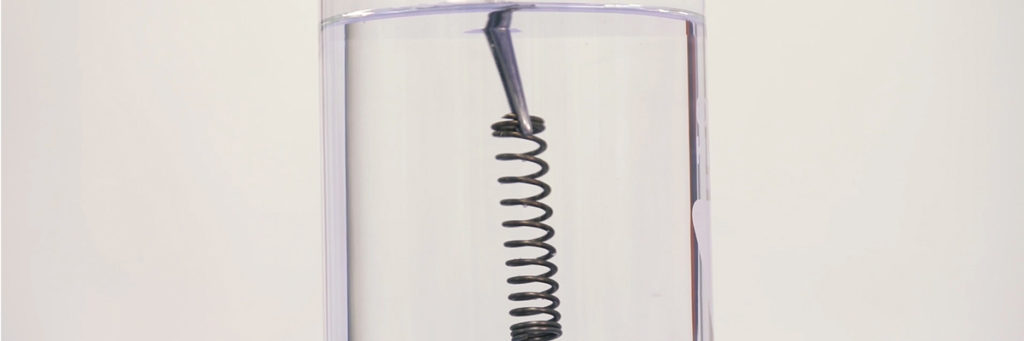
Functional stability
As already described in the section applications, your shape memory alloy is also always subject to a degree of fatigue which highly depends on your design and load function. Additionally, other factors prevail that are by and large owed to microstructural reasons. Many factors that play a role in fatigue considerations can however be excluded or avoided altogether by the right choice of process parameters and by ensuring the SMA elements’ correct use in the installed state. In the SMA course you will find more material on this aspect. Ultimately, you will be interested in designing your shape memory alloys specifically for your application and for achieving exactly your desired forces. So once the characteristic values are secured, such as by cyclic temperature tests, the design can be undertaken bearing only costs in mind.
Biocompatibility & resistance to corrosion
Nickel titanium SMA components are inherently biocompatible and therefore they are approved as material for implants. Being from the industry, you will already know that they are being used as stents, dental wire wires, root canal files or guide wires in surgical devices. On the one hand, NiTi shape memory alloys exhibit a thin oxide film which makes the component resistant to corrosion.
On the other hand, the high nickel content does not constitute an obstacle due to the high bonding forces within the material. Titanium, usually highly reactive, binds the nickel to an unusually high extent. Investigations under comparable test conditions. You will find a more detailed example of this in the free course.
The mechanical and physical properties of SMA
In the properties section of the course you will learn:
- details on the phase transformation during heating and cooling
- material parameters which are of great importance for design and interpreting behaviour
- at what point thermal hysteresis forms and what this implies for your application
- how to know and interpret in detail
- which other circumstances influence the functional stability of your solution
- why NiTi SMA are resistant to corrosion and approved as an implant material
So get your free course as a PDF now and refresh your knowledge about SMA at any time using the included summary. This helps you in discussion when thinking about the use of shape memory alloys in your application.
Let’s recap what we’ve learnt in this section:
- When dealing with NiTi-SMA, characteristic values from the standard tensile test usually play a minor role
- Important (thermal) characteristic parameters for actuator systems in SMA are AS, AF, Ap, Ms, Mf and Mp
- The temperature- and time related sequence of the structural transformation during heating is not a mirror image of the characteristic profile when reshaping (thermal hysteresis)
- NiTi are biocompatible and resistant to corrosion due to a thin oxide layer