German economy nominates Ingpuls as Innovator of the Year 2020
Following our award as TOP Innovator of the Year 2019, we are pleased to announce that we have also been nominated for Innovator of the Year 2020. This competition is organised by DDW (Die Deutsche Wirtschaft). Next year, the audience award will be presented to all nominees during the Innovation Festival in Essen.
Quantum leap in materials research opens up new possibilities for medical technology
NiTi shape memory alloys are the daily business of the technology company Ingpuls. The Bochum-based materials specialists have succeeded in producing nickel-titanium materials with particularly low impurity levels in record time using conventional process technology. Semi-finished products with properties never thought possible are already the result. The service life of implants such as heart valve or aortic stents could also be dramatically extended.
Shape memory alloys (SMA for short) are now state of the art in modern medical technology: whether as dental tension wire, in root canal files, as guide wires in catheters or the famous stents. However, the production of medical products from SMA is a complicated process. Many different companies have developed specialised knowledge in this area over the decades and made continuous progress to establish functioning and stable supply chains. A market emerged that today has a volume of around 16 to18 billion US dollars. What has not changed for a long time, however, is the quality of the raw material from which these high-tech products have been made so far.
Prof. Dr. Nikolaus Franke, the scientific director of TOP 100, is impressed by the award-winning medium-sized companies. “The TOP 100 companies have consistently geared themselves to being as innovative as possible,” he notes. On 26 November there will be another reason to celebrate: then all the award winners of the current TOP 100 year will come together to receive congratulations from Ranga Yogeshwar at the 7th German SME Summit in Ludwigsburg. The science journalist has been mentoring the innovation competition for ten years.
High-purity materials from nickel-titanium production in Bochum
At the beginning of the process chain is the melting process. Here, many properties of the future products are already irrevocably determined. For example, the quantities of impurities such as carbon or oxygen. Through the subsequent processing of the material, the size and distribution of these unavoidable accompanying elements are also determined for the final semi-finished wire or tube. By transferring knowledge from automotive series production to medical technology, Ingpuls has now succeeded in reducing the size of these precipitates by a factor of ten or more. This has a significant impact on the processability of the material and thus the properties of the medical products to be manufactured.
In order to qualify the new material quality for use in medical devices, Ingpuls has now been working with almost two dozen different medical technology companies since the end of last year. This qualification phase can be relatively short, for example for endodontic applications or guide wires. But it can also take many years when it comes to approval for the use of permanent implants. After a successful start, the company is optimistic about gaining a foothold in medical technology and establishing another foothold on the market and product side.So far, only three SMA manufacturers worldwide have even been able to achieve the high purity standards for nickel-titanium material in medical technology, two of them in the USA, one in Japan. The corona pandemic has already led many places to scrutinize existing supply chains more critically than before. Ingpuls, a company based in Bochum, Germany, is now establishing another serious alternative for securing the supply of high-quality shape memory metals.
To this end, Ingpuls has taken precautions in terms of capacity and has already significantly increased its development and production capacities by moving into a new company location in July this year. Up to 60t of NiTi-SMA can be produced and processed in the Ruhr region from 2021. Whether this will be enough after the latest technological leap is no longer clear. Another doubling of capacity by 2026 to then 120t per year is under discussion following discussions with medical technology customers. Exciting developments lie ahead.
You know Nitinol® as an established material in medical technology. But due to modified alloys and manufacturing processes, shape memory alloys offer you completely new opportunities. Don’t be limited by the standard functions of this super elastic material: Expand the spectrum of your possibilities and create entirely new functionalities!
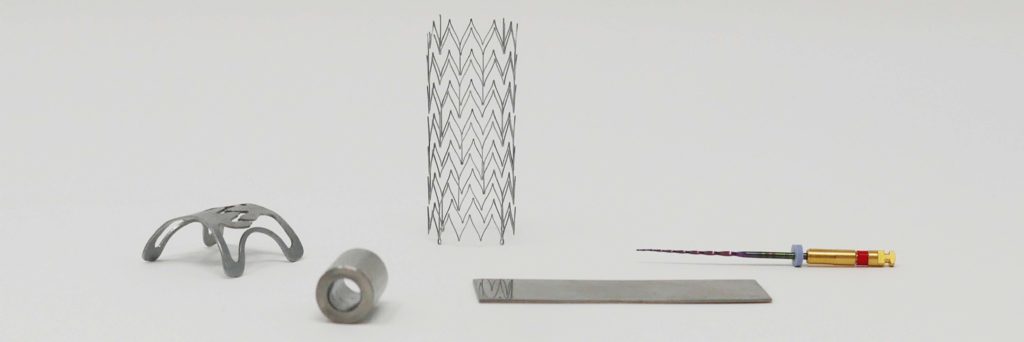